The Science Behind Porosity: A Comprehensive Overview for Welders and Fabricators
Recognizing the elaborate systems behind porosity in welding is crucial for welders and producers aiming for flawless craftsmanship. From the structure of the base materials to the intricacies of the welding procedure itself, a plethora of variables conspire to either worsen or alleviate the presence of porosity.
Comprehending Porosity in Welding
FIRST SENTENCE:
Evaluation of porosity in welding exposes critical understandings right into the integrity and high quality of the weld joint. Porosity, characterized by the visibility of dental caries or spaces within the weld metal, is a common worry in welding processes. These voids, otherwise effectively addressed, can endanger the architectural stability and mechanical residential properties of the weld, causing possible failures in the completed product.
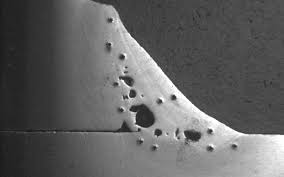
To discover and measure porosity, non-destructive testing approaches such as ultrasonic testing or X-ray evaluation are commonly used. These methods allow for the identification of inner issues without jeopardizing the honesty of the weld. By assessing the size, form, and circulation of porosity within a weld, welders can make informed decisions to improve their welding processes and achieve sounder weld joints.

Variables Affecting Porosity Formation
The incident of porosity in welding is affected by a myriad of elements, ranging from gas protecting efficiency to the ins and outs of welding parameter settings. One vital aspect adding to porosity development is inadequate gas securing. When the shielding gas, commonly argon or carbon dioxide, is not effectively covering the weld swimming pool, atmospheric gases like oxygen and nitrogen can contaminate the liquified metal, resulting in porosity. Additionally, the tidiness of the base materials plays a substantial function. Pollutants such as rust, oil, or dampness can vaporize during welding, producing gas pockets within the weld. Welding criteria, consisting of voltage, present, take a trip rate, and electrode type, additionally impact porosity development. Utilizing improper setups can generate excessive spatter or warmth input, which subsequently can result in porosity. Moreover, the welding strategy utilized, such as gas metal arc welding (GMAW) or protected metal arc welding (SMAW), can affect porosity development as a result of variations in warmth distribution and gas protection. Understanding and controlling these factors are vital for decreasing porosity in welding operations.
Results of Porosity on Weld Top Quality
Porosity formation substantially jeopardizes the structural integrity and mechanical residential or commercial properties of welded joints. When porosity exists in a weld, it creates gaps or dental caries within the material, decreasing the total toughness of the joint. These spaces serve as tension focus factors, making the weld much more at risk to splitting and failure under lots. The presence of porosity likewise deteriorates the weld's resistance to rust, as the caught air or gases within the gaps can respond with the surrounding environment, leading to deterioration with time. Furthermore, porosity can hinder the weld's ability to hold up against pressure or influence, additional endangering the general quality and integrity of the bonded structure. In important applications such as aerospace, automotive, or architectural constructions, where safety and longevity are extremely important, the this post detrimental results of porosity on weld quality can have extreme consequences, emphasizing the importance of minimizing porosity through appropriate welding techniques and procedures.
Methods to Minimize Porosity
Additionally, utilizing the ideal welding specifications, such as the right voltage, present, and take a trip speed, is crucial in stopping porosity. Maintaining a consistent arc size and angle throughout welding likewise assists lower the chance of porosity.

Using the suitable welding technique, such as back-stepping or using a weaving activity, can also help distribute warm Recommended Site evenly and lower the chances of porosity development. By applying these methods, welders can efficiently lessen porosity and generate top quality welded joints.
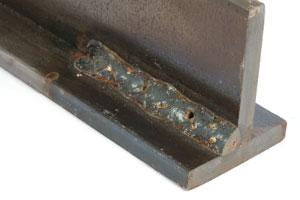
Advanced Solutions for Porosity Control
Carrying out innovative modern technologies and innovative approaches plays a pivotal duty in attaining premium control over porosity in welding procedures. Furthermore, utilizing innovative welding strategies such as pulsed MIG welding or changed environment welding can also assist mitigate porosity problems.
An additional sophisticated option involves making use of sophisticated welding devices. Utilizing equipment with built-in attributes like waveform control and sophisticated power sources can boost weld high quality and decrease porosity risks. The execution of automated welding systems with accurate control over criteria can significantly lessen porosity defects.
Moreover, including sophisticated tracking and examination modern technologies such as real-time X-ray imaging or automated ultrasonic testing can aid in finding porosity early in the welding procedure, permitting for instant corrective activities. Generally, incorporating these innovative solutions can greatly improve porosity control and enhance the total top quality of bonded elements.
Final Thought
In verdict, comprehending the science behind porosity in welding is necessary for welders and makers to produce high-quality welds - What is Porosity. Advanced solutions for porosity control can further enhance the welding procedure and guarantee a hop over to these guys strong and trusted weld.
Comments on “What is Porosity in Welding: Essential Tips for Getting Flawless Welds”